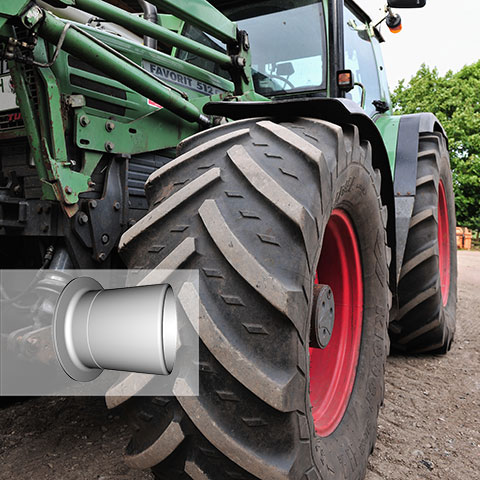
Shaft Repair Sleeves
are metallic sleeves and are used as counterface replacement for radial shaft seals.
Applications
Shaft repair sleeves are pushed onto shafts to repair the worn counterface for radial shaft seals. They are a quick and cost-effective alternative to replacing or often costly reworking of the shaft.
Shaft repair sleeves can also be used as original equipment to eliminate the need for costly machining of the shaft surface.
Special features / advantages
- Quick and easy installation
- Cost-effective renewal of worn shaft surface
- Minimizes repair and downtime
- Thin wall thicknesses do not require a change in seal dimensions
- Precisely ground surface ensures long service life
- High availability for many common dimensions
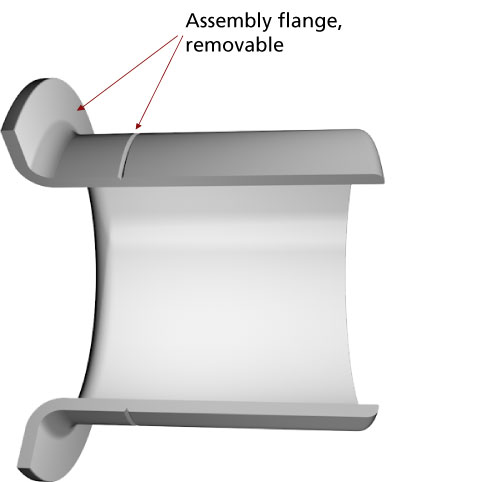
Technical data
Surface finish/roughness
Ra = 0.2 - 0.8 µm
Rz = 1 - 5 µm
Rmax ≤ 6.3 µm
Surface machining
free of orientation, non-directionally ground
Surface hardness
HV 220 (95 HRB) wear-resistant machining
Wall thickness
0.28 mm (0.011 inch) thin-walled design
Materials
Material sleeve
stainless steel 1.4301 (AISI 304)
Material assembly tool
depending on version in standard steel / aluminium
Application parameters
The operating parameters are specified by the seal and are usually not limited by the shaft sleeve.
Assembly
Shaft sleeves can be installed quickly and easily using the supplied assembly sleeve. The notched, detachable assembly flange is easy to remove. Assembly instructions are included in the packaging.
- Clean the worn counterface surface on the shaft. Remove unevenness with emery fleece or a fine file.
- Measure the diameter of the seal counterface surface in an undamaged area. Select the suitable sleeve size based on this value.
- Place the sleeve on the top of the shaft with the flange first.
- Place the supplied assembly sleeve against the flange of the sleeve. If the assembly sleeve is too short, a pipe can be used instead.
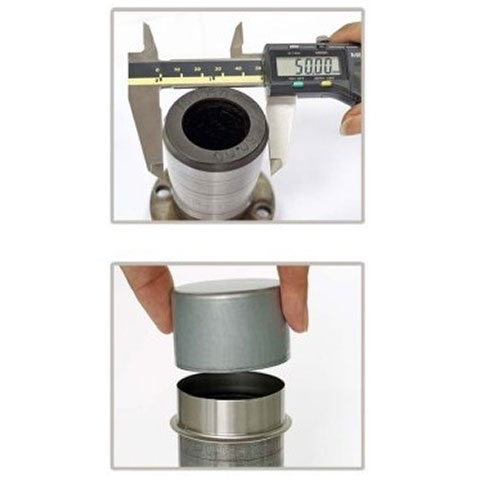
- Gently tap the center of the assembly sleeve until the sleeve covers the worn area.
- The sleeve flange does not need to be removed unless it interferes with the application. If it must be removed, a cut should be made in the sleeve flange before assembly. The cut should end at the tearing groove. The pre-cut process and the flange removal must be done carefully to avoid damaging the outside diameter of the sleeve.
- Check again if there are burrs on the sleeve that could damage the seal.
- Lubricate the sleeve.
- Proceed with the installation of the seal.
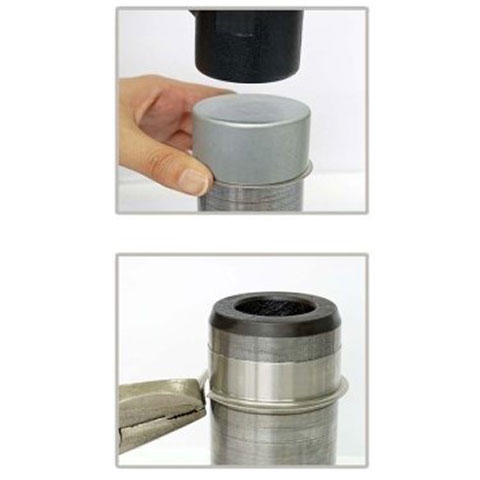
Downloads
Please find here the technical information summarized in PDF format as well as the lists of available inch and metric dimensions.
anyseals – navigating tariffs with you!
We increased stock levels to give you continued availability at attractive and stable prices!
Login for availability and prices or reach out to us if you need help
☎ (216) 676-9934